게이트 크기 최적화 및 로션 펌프 사출 금형의 위치 금형 흐름 분석을 통한 시뮬레이션, 분석 및 설계 조정의 체계적인 프로세스가 포함됩니다. 이 최적화를 달성하기 위한 단계별 가이드는 다음과 같습니다.
1. 프로젝트 목표 및 기준 정의:
- 로션 펌프 사출 금형의 목표와 기준을 명확하게 정의하는 것부터 시작하십시오. 부품 품질, 주기 시간, 재료 사용량, 비용 제약과 같은 요소를 고려하십시오.
2. 중요 데이터 수집:
- 사출 성형 공정에 사용되는 특정 플라스틱 수지에 대한 정확한 재료 데이터를 얻습니다. 여기에는 용융 흐름 지수(MFI), 점도, 열 특성 및 기타 재료 특성이 포함됩니다.
3. 모델 생성:
- 캐비티, 코어, 냉각 채널 및 러너 시스템을 포함하여 로션 펌프 부품과 사출 금형의 상세한 3D 모델을 생성합니다. 모델이 의도한 생산 조건을 정확하게 나타내는지 확인하십시오.
4. 시뮬레이션 설정:
- 금형 흐름 분석 소프트웨어를 활용하여 시뮬레이션을 설정합니다. 사출 압력, 온도 프로파일, 냉각 속도 등의 사출 성형 공정 매개변수를 정의합니다. 게이트 위치와 초기 게이트 크기를 지정합니다.
5. 초기 시뮬레이션 실행:
- 선택한 게이트 위치와 크기로 초기 금형 흐름 시뮬레이션을 실행합니다. 충전 시간, 압력 분포, 웰드라인, 에어 트랩 위치를 포함한 결과를 분석합니다. 잠재적인 문제나 개선이 필요한 영역을 식별합니다.
6. 게이트 위치 분석:
- 선택한 게이트 위치의 적합성을 평가합니다. 균형 잡힌 캐비티 충전, 외관상의 결함 방지, 웰드라인 영향 최소화 등의 요소를 고려하세요. 필요에 따라 게이트 위치를 조정합니다.
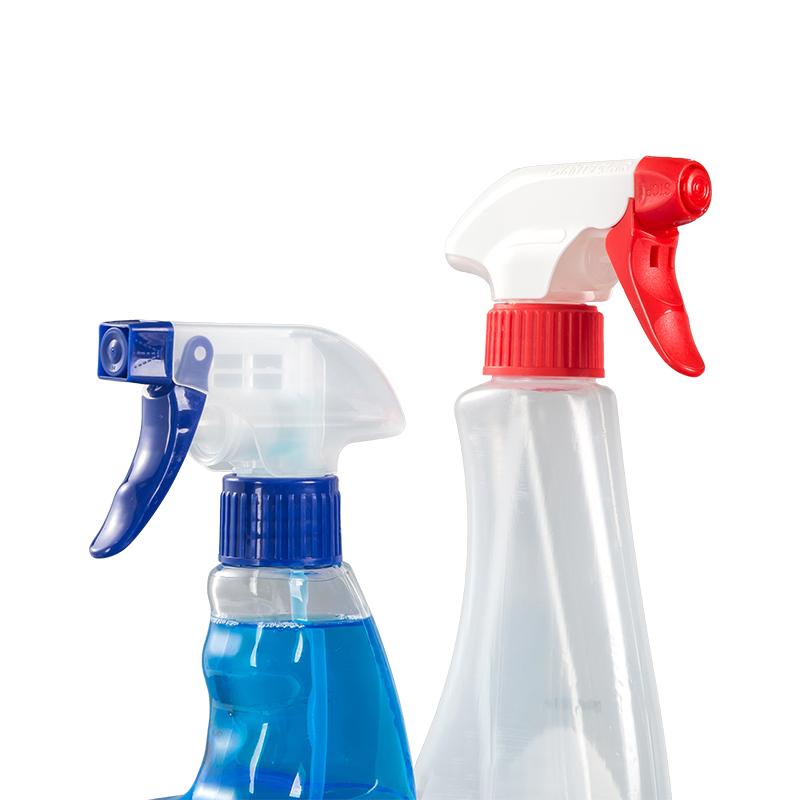
7. 게이트 크기 분석:
- 게이트 크기가 사출 공정에 미치는 영향을 분석합니다. 후속 시뮬레이션에서 게이트 크기를 점진적으로 늘리거나 줄여 결함을 일으키지 않고 충전 시간, 압력 및 재료 흐름의 균형을 맞추는 최적의 크기를 찾습니다.
8. 게이트 유형 선택:
- 게이트 크기 분석 결과에 따라 스프루 게이트, 엣지 게이트, 팬 게이트 등 적절한 게이트 유형을 선택합니다. 게이트 유형은 재료가 캐비티에 들어가는 방식과 부품 품질에 영향을 줄 수 있습니다.
9. 러너 시스템 최적화:
- 모든 캐비티에 재료가 고르게 분포되도록 러너 시스템 설계를 최적화합니다. 재료 낭비와 압력 강하를 최소화하려면 러너 치수와 구성을 조정하십시오.
10. 냉각 채널 분석:
- 게이트 위치와 크기가 냉각 효율에 미치는 영향을 평가합니다. 선택한 게이트 구성이 냉각 채널의 효율성을 방해하지 않는지 확인하십시오. 필요한 경우 냉각 채널 배치를 조정합니다.
11. 반복 시뮬레이션:
- 반복적인 시뮬레이션을 수행하여 분석 결과에 따라 게이트 위치와 크기를 점진적으로 조정합니다. 균형 잡힌 충전, 결함 최소화 등 원하는 기준이 충족될 때까지 계속해서 디자인을 개선합니다.
12. 최종 검증:
- 최적화된 게이트 크기와 위치를 검증하기 위해 최종 금형 흐름 분석을 수행합니다. 설계가 사전 정의된 프로젝트 목표 및 기준을 충족하는지 확인합니다.
13. 문서화 및 보고:
- 선택한 게이트 구성, 시뮬레이션 데이터 및 설계 조정을 포함한 결과를 문서화합니다. 최적화 프로세스와 그 결과를 요약한 보고서를 준비하세요.