사출 성형은 용융된 플라스틱 재료를 금형 캐비티에 주입하여 플라스틱 부품을 생산하는 데 사용되는 제조 공정입니다. 이 공정에 사용되는 금형을 사출 금형 또는 사출 성형 도구라고 합니다.
사출 금형은 플라스틱 부품의 원하는 모양과 치수를 만들기 위해 정밀하게 설계된 맞춤형 도구입니다. 일반적으로 강철 또는 알루미늄으로 만들어지며 코어와 캐비티의 두 부분으로 구성됩니다. 코어와 캐비티는 원하는 부품의 네거티브 형상으로 설계되었으며, 이들이 합쳐지면 완전한 금형 캐비티를 형성합니다.
사출 성형 공정에는 다음 단계가 포함됩니다.
플라스틱 소재 선택 : 강도, 유연성, 내열성, 외관 등 특성을 고려하여 원하는 부품에 적합한 플라스틱 소재를 선택합니다.
금형 준비: 사출 금형 검사, 세척 및 생산 준비가 완료되었습니다. 여기에는 적절한 냉각 채널, 이젝터 핀 및 기타 필요한 기능이 있는지 확인하는 것이 포함됩니다.
사출: 일반적으로 작은 펠렛이나 과립 형태의 플라스틱 재료를 녹여 고압 하에서 금형 캐비티에 주입합니다. 사출은 사출성형기라 불리는 특수 기계에 의해 수행됩니다.
냉각: 용융된 플라스틱이 금형 캐비티에 주입되면 냉각 및 응고되어 금형 캐비티의 모양을 갖게 됩니다.
배출: 플라스틱이 응고된 후 금형 절반이 분리되고 이젝터 핀이나 기타 메커니즘을 사용하여 부품이 금형에서 배출됩니다.
후처리: 배출된 부품에는 초과 재료 다듬기, 표면 마감 또는 조립과 같은 추가 후처리 단계가 필요할 수 있습니다.
사출 성형은 높은 정밀도와 효율성으로 복잡한 형상을 생산할 수 있는 능력으로 인해 다양한 산업 분야에서 널리 사용됩니다. 자동차 부품, 소비재, 의료 기기, 전자 제품 등 다양한 제품을 제조하는 데 일반적으로 사용됩니다.
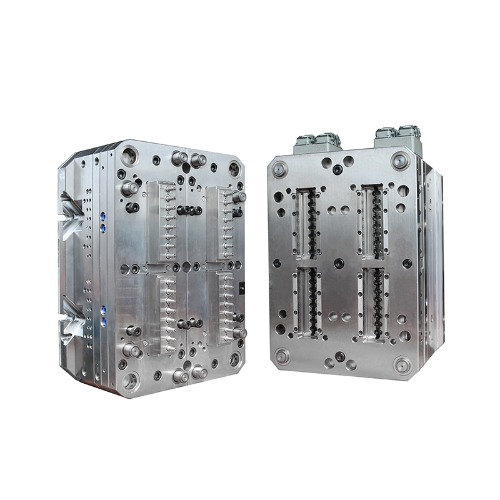